Contents
Whether you are a construction worker or not, you probably realized that cement is almost everywhere we go, especially if you live in a city with tall skyscrapers and solid sidewalks.
But what is cement, actually? What is it made of? How is it made?
In this article, we will cover all you need to know about cement, from its chemical composition to its manufacturing process, including the different types of cement, and the difference between cement and concrete.
What Is Cement?
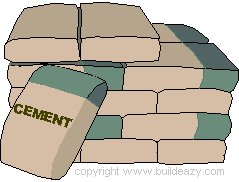
Cement is a substance that is mainly used in construction that has dated as far back as the Roman Empire and today is still used as one of the most prevalent materials used for building. This is because cement works very well with binding other materials together because it sets and hardens which makes for a very strong bind.
Cement has what is called a high compressive strength which means that it can put up with a lot of weight without changing its shape or moving in any way. However, cement has a low tensile strength which means it cannot withstand being pulled or stretched a lot without breaking, this means that it needs to have fibrous materials added in order to reinforce it.
This gives cement the label ‘binder’ which is the term used for material or substance such as cement that holds materials together to make a whole. Binders tend to all work in the same way, which is starting off as a liquid, doughy material before it hardens, there are two categories of binders, organic and inorganic which include cement.
How Is Cement Made?
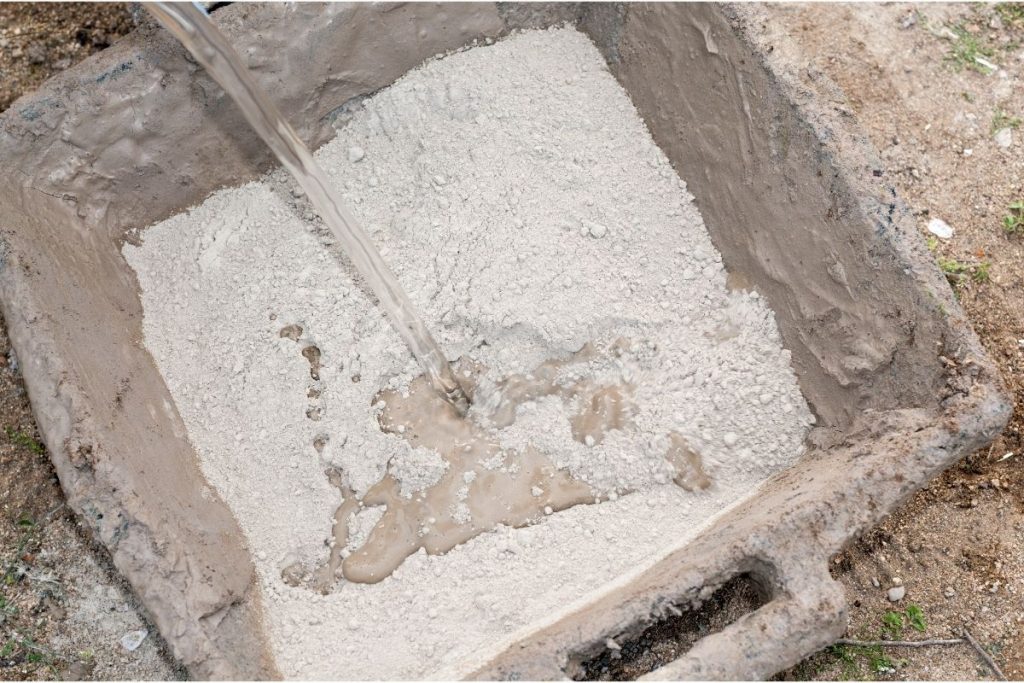
Cement is a lot more chemically involved than a lot of people may think, and the strength, curing time, the heat of hydration, and sulfur resistance depends a lot on what chemicals have been used and by what amount.
Therefore, the manufacturing process is closely controlled, and the common ingredients include shells, limestone, chalk, clay, slate, iron, ore, silica sand, and blast furnace slag which is a by-product from the production of iron in blast furnaces.
These ingredients are then combined and heated at a high temperature which makes the cement form a substance similar to a rock that is then ground down into a fine powder that is what we know as cement. Vertical steel mills are used to grind these materials down and with three conical rollers which apply a lot of pressure.
After this, big rotary kilns are used to transform the mixture into a substance called clinker which is small gray nodules measuring at about four centimeters in diameter. Steel balls varying in size are used to grind down the clinker as it moves its way through the two chambers.
The cement is ground so fine that it contains 150 billion grains in just one pound of cement, at this stage, it is ready for transportation to companies to be used in a wide range of construction projects.
This way of making cement is known as the dry process and is the most popular way for cement to be manufactured. However, there are some kilns that use the wet process which means that water is used to grind the raw materials before they are put into the kiln.
Types Of Cement And What They Are Used For
Cement is mostly used in construction and there are many different types of cement that can be used depending on the type of work that needs to be done.
The type of cement that is used in construction is usually inorganic and can be categorized as either non-hydraulic cement or hydraulic cement.
Non-Hydraulic Cement
Due to the use of lime, oxychloride, and gypsum platers used in this type of cement, in wet conditions or underwater, it cannot set and instead does so when it comes into contact with carbon dioxide in the air. However, once it has been set and strengthened in dry conditions, it is non-reactive to any chemicals.
Non-hydraulic cement was the first type of cement that was invented and is not as commonly used because it is less practical and convenient in most applications. For example, a lot of construction work is done outside so if you are using non-hydraulic cement and it starts to rain, you will not be able to continue until it has stopped raining and the cement can get dry again.
Its lack of versatility and practicality is one of the biggest reasons as to why it is becoming less common, but in some stonework and mortar use, it is still used frequently because this usually takes place indoors.
Hydraulic Cement
With non-hydraulic cement becoming more obsolete over the years, a new type of cement has taken the front seat which is called hydraulic cement. As of today, it is the most commonly used variation and is made using limestone, gypsum, and clay which are combined at a very high temperature.
When this type of cement was created, it was made with convenience and practicality in mind which is why it is easy to apply and has a very fast drying time. This is due to its ingredients which form stable calcium silicate hydrates when they react with water, causing it to almost instantly harden when it is poured – even in wet conditions.
Portland Cement
Since Portland cement is one of the most commonly used cement, we will focus a bit more on it and talk about the different types of Portland cement which have been categorized by the ASTM and talk about how they are made and what they are used for.
Portland cement is one of the most popular types of hydraulic cement used in construction and building, it dates back to the 19th century and the ingredients consist of clay and limestone which is combined at a very high temperature before being added to water. Portland cement is a caustic material meaning that it has the ability to chemically burn your skin if you are not handling it with enough care.
Portland cement can be used on its own or as a mixer with other components, allowing you to achieve dense and smooth surfaces for things such as sidewalks or indoor warehouses. It can also be used in brickwork if it is combined with other compounds as it makes it into a strong binding agent.
The American Society for Testing and Materials or ASTM has come up with different ways to classify Portland cement, depending on the type of use they have. These types range from type I to V and depending on the requirements of the job, you can make the choice between what type to use.
- Type I is the best choice for general construction and has an acceptable strength and a low heat of hydration which is when the cement is mixed with water and heat is released. It is usually used for floors, bridges, sewers, pipes, and reinforced buildings just to name a few.
- Type II has a lot of the same uses as type I but generates a bit more head of hydration but at a slower rate and is resistant to sulfur attacks which makes it a popular choice in both Canada and the western USA because they have conditions that are rich in sulfur.
- Type III is almost the exact same to type I chemically but it has a shorter curing time, meaning it takes less time to get hard. This is partly due to the fact that it grounds finer and has a higher amount of tricalcium silicate. As well as this, it gets stronger faster than type I and works well for construction that requires the cement to set quickly so that the project can be finished quickly and put to use.
- Type IV was made so that it didn’t release as much heat during hydration which is done by slightly altering the ingredients.
However, this comes at a price because the cement does not have as much strength as the other types of Portland cement but can still be utilized for pieces of construction that have a low surface-to-volume ratio such as gravity dams.
This is because if the cement had a higher amount of heat during hydration, it could result in cracks in the dam which can have devastating effects.
Finally, type V has lots of similarities to type II but has a much higher tolerance to sulfur attacks. This is achieved by lowering a particular chemical called C3A to lower than 5%. This makes it suitable for structures that are buried underground where they may come into contact with sulfur-rich ions.
In concrete construction, there are up to 13 different types of cement that each have their advantages and disadvantages.
Is Cement The Same Thing As Concrete?
The terms cement and concrete seem to be used to refer to one another in day-to-day talk but the average person may not be aware that cement is an ingredient to concrete and they are not the same thing.
Concrete is made from a mixture of paste and aggregates with the paste being water and Portland cement and the aggregates being gravel, sand, and crushed stone. If you are one of those who use cement and concrete interchangeably, don’t feel bad because it has been a common occurrence for 600 years!
Cement production illustrated
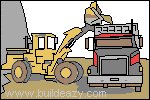
1.) Limestone is taken from a quarry. It is the major ingredient needed for making cement. Smaller quantities of sand and clay are also needed. Limestone, sand, and clay contain the four essential elements required to make cement. The four essential elements are calcium, silicon, aluminum, and iron.
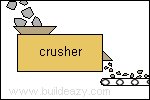
2.) Boulder-size limestone rocks are transported from the quarry to the cement plant and fed into a crusher which crushes the boulders into marble-size pieces.
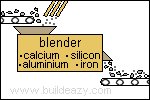
3.) The limestone pieces then go through a blender where they are added to the other raw materials in the right proportion.
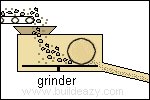
4.) The raw materials are ground to a powder. This is sometimes done with rollers that crush the materials against a rotating platform.
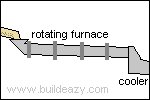
5.) Everything then goes into a huge, extremely hot, rotating furnace to undergo a process called “sintering”. Sintering means: to cause to become a coherent mass by heating without melting. In other words, the raw materials become sort of partially molten. The raw materials reach about 2700° F (1480°C) inside the furnace. This causes chemical and physical changes to the raw materials and they come out of the furnace as large, glassy, red-hot cinders called “clinker”.
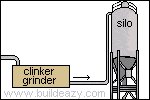
6.) The clinker is cooled and ground into a fine gray powder. A small amount of gypsum is also added during the final grinding. It is now the finished product – Portland cement.
The cement is then stored in silos (large holding tanks) where it awaits distribution.
The cement is usually shipped in bulk in purpose-made trucks, by rail or even by barge or ship. Some is bagged for those who want small quantities.
A video on how cement is made
Interactive 3d Cement Plant
As you stayed with me until the end of this article, I think you deserve this Interactive 3d Cement Plant to play with 😅
thank you,I found the information beneficial, hope it will help me in future.
thanks i apreciate this information and i hope it will be usefull to me as young civil engineer to be
Thanks for garding me in my cuase of study.
Good page
Thanks very much for sharing this with us. It has helped those of us who had no idea about how this was made.
Very useful and educational exposé thank you very much
what if i mix lime (bought in a bag from the store)
with sand and water?? Will it harden into a solid mass??
But will exposure to water cause the solid mass to melt, dissolve over time ??!!
thanks you for tell those of use who didn’t know how cement was made
seti alpha Why the uninformed outburst ?
Cement is cement, water, sand, lime and aggregate are added to produce plaster , mortar, concrete etc ! Keep yourself civil mate , people are asking legitimate questions, which doesn’t make them morons