Contents
Epoxy resin is becoming more and more used in current times, with more people using it for creative and constructive means. It is known for its many strong qualities that make it very secure and stable in construction and in art.
You have probably seen countless TikTok’s and Instagram Reels of people using epoxy resin on wood to create gorgeous tables, memoirs, artwork, and even to create new, more durable flooring and household items.
The truth is that while epoxy is known mainly for a few specific purposes, it actually has countless uses, making it one of the most variable and durable commonly used materials available to us at this point in time.
Let’s take a little time to appreciate it, learn about it, its varieties, uses, and what is so good about it.
What Is Epoxy Resin?
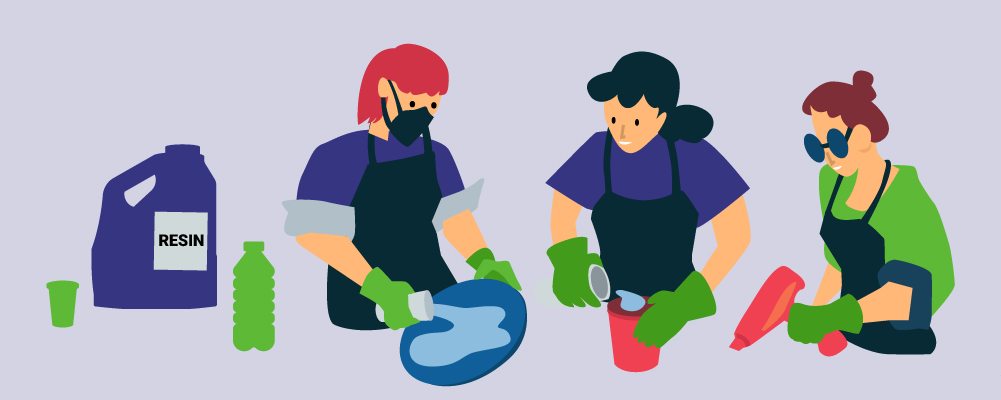
Epoxy resins are actually reactive polymers and pre-polymers that contain something known as epoxide groups.
Epoxies actually react with themselves, once you have applied a catalyst or a co-reactant such as amines or phenols to them.
In comparison to a lot of other resin types, a cured epoxy will have superior mechanical properties, and it will also have a great deal more thermal resistance as well as chemical resistance.
Hence, it’s been more heavily used in recent years.
The fact that epoxy resins are so versatile makes them very effective in a variety of applications. They can be useful in electrical insulation, adhering structural parts, coating concrete, and so on.
Although it does depend on the type of epoxy you use, as a whole epoxy can be used on a wide variety of materials. It can be used on stone, plastic, metal, and also wood.
You can use it in many different ways, for a multitude of reasons.
How To Use Epoxy Resin Safely
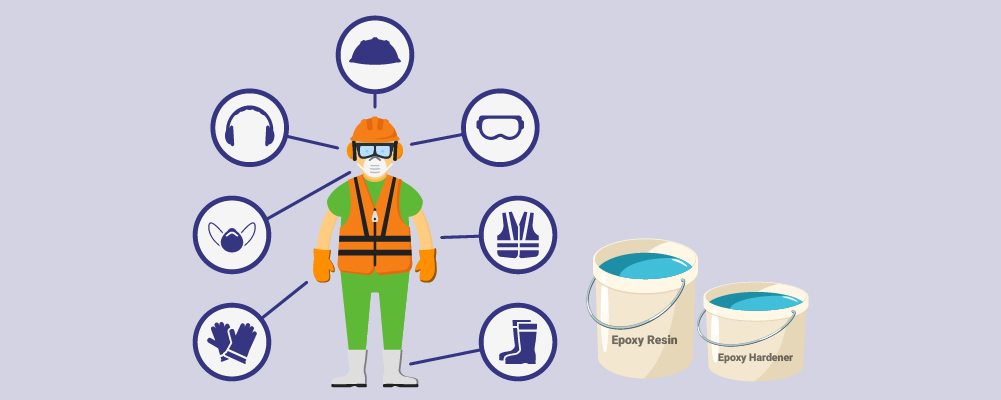
We would be remiss if we told you that epoxy resin is safe to use from the get-go. It is not, there are a wide variety of different safety precautions that you should take when you use epoxy resin.
First of all, you should always wear gloves when you use epoxy resin to keep your hands safe from any exposure to the resin and any hardener liquids used.
Nitrile gloves are the highest recommended for this use as they are rather less unlikely to react upon any contact with skin or resin.
Baby wipes can also remove any resin that ends up in contact with your skin. Soap and water should be used to remove any further resin.
You should also wear a plastic apron to ensure that spilled resin is easily removable. Safety goggles should also be worn to protect your eyes.
If it does get in your eyes, however, you need to flush them on repeat with water over a fifteen-minute period and seek out medical attention.
Whenever you use epoxy resin, always make sure that there is enough ventilation and airflow. You can also use a respirator if you are otherwise unable to increase the airflow in the room you are using epoxy in.
If you can increase the ventilation in the room that you are working in, it is a good idea to switch on a ceiling fan or air conditioning unit, open windows, or get standing fans. However, open windows are the best recommendation.
It is always good to have a respirator just encase as fumes can be released from epoxy, which can be toxic. It is better to be safe than sorry.
Always browse ideal PPE before you start working with epoxy, and make sure you have all you need for your own safety.
What Are The Different Types Of Epoxy Resins?
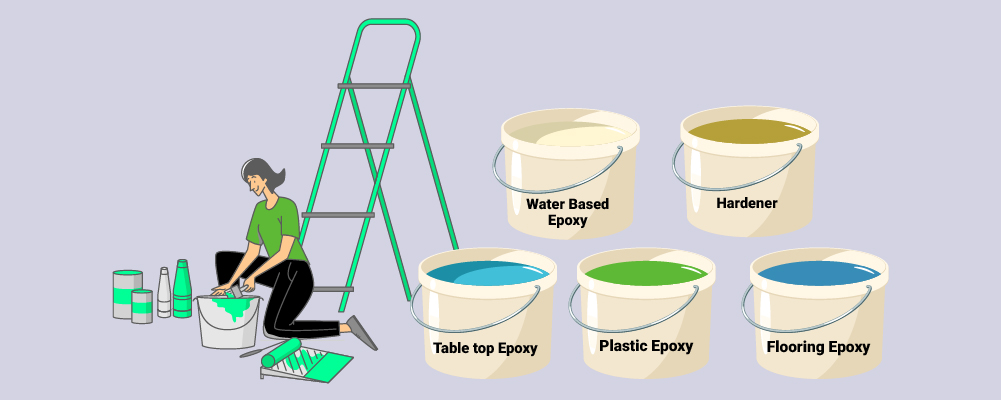
Epoxy resins will be categorized by the different chemical chains that the reactive epoxy group will be bonded to. It falls into one of two main categories, these are glycidyl and non-glycidyl.
A resin that falls under the glycidyl category will be diglycidyl-ether, glycidyl-ester and glycidyl-anime.
If a resin is non-glycidyl then it can be aliphatic, or it could be cyclo-aliphatic.
The most commonly used of all epoxies is usually glycidyl-ether epoxies. Those which are of the novolac and bisphenol variety are the most common still.
While there are many more different types of epoxies, we want to focus on 6 primary types that are the most commonly used.
These are:
- Bisphenol epoxy resin.
- Aliphatic epoxy resin.
- Novolac epoxy resin.
- Cycloaliphatic epoxy resin.
- Glycidylamine epoxy resin.
- Epoxy resin diluents.
Let’s look a little more into these 6 primary types of resin that are most commonly used.
Aliphatic Epoxy Resins
The first is Aliphatic epoxy resins. These resins are made through a double boned epoxidation. They can be made this way, or they can also be made via a reaction with epichlorohydrin.
The double bonded epoxidation will usually involve cycloaliphatic epoxides and a form of epoxidized vegetable oils. These cycloaliphatic epoxides will usually feature 1 or more aliphatic rings in their molecule that will contain the oxirane ring.
They have a higher defined aliphatic structure, an absence of any chlorine and a very high orirane content.
This makes them very good for low-level viscosity, weather resistance, and minimal dielectric constants, and they also have a very high T g.
Cycloaliphatic Epoxy Resins
Speaking of cycloaliphatic epoxies. This is a type of epoxy that has a single or more aliphatic rings inside their epoxy ring molecule.
They have a very obvious and distinct aliphatic structure, no chlorine, and a very high amount of oxirane.
This is a chemical structure that will result in a lower level of viscosity, strong weather resistant abilities, lower dielectric constants, and a very high glass transition temperature (the aforementioned T g).
Bisphenol Epoxy Resins
Bisphenol epoxy resin, otherwise known as Disphenol-A diglycidyl ether (DGEBA) is a very popular resin when it comes to commercial application.
It is a resin formed from a reaction between epichlorohydrin and bisphenol-A while a basic catalyst is present.
While it is a good epoxy resin, this variety is also the one that has the lowest molecular weight of them all.
Novolac Epoxy Resins
Novolac resins are made with a much stronger functioning in order to strengthen the cross-linked density of the eventually cured system.
Having this makes them extra ideal for higher temperature uses that may also need to have a high to extreme chemical resistance.
Novolac epoxies will also not contain any volatile organic compounds or any solvents, so they are actually even more safe to use than some others!
These resins are actually made as a result of a reaction and contact between methanol formaldehyde and phenol.
The reaction of the novolacs and the epichlorohyrdin will result in the forming of this epoxy with glycidyl residue including EPN or ECN.
While formaldehyde is rather present in the creation of this epoxy, it is actually free of any VOC’s, so they are crazy safe for using, and you do not even need to use a respirator to work with them.
They are also fantastic adhesives as well!
Glycideylamine Epoxy Resins
This type of epoxy has a high level of functionality. They are made from the reaction between epichlorohydrin and aromatic amines.
Both triglycidyl-p-aminophenol as well as N, N, N, N’ tetraglycidyl-is-(4 aminophenyl) methane are all industrial grades which have a low to medium viscosity when at room temperature, this makes them easier to process overall.
They are overall easier to process than ECN or EPN varieties when they are at room temperature.
Epoxy Resin Diluents
Epoxy resin diluents are crafted from aliphatic alcohols or sometimes polyols. These epoxies can be difunctional, monofunctional, or of greater functionality.
(Monofunctional=dodecanol glycidyl ether, Difunctional= butanediol diglycidyl ether, Higher functionality= trimethylolpropane triglycidul ether).
These very reactive diluents are often used in concrete coatings, adhesives, composites, and metal coatings, as well as for repair and building compounds.
They can be used on the resin side or curing agent side for creating optimal flexibility.
Key Properties Of Epoxy resins
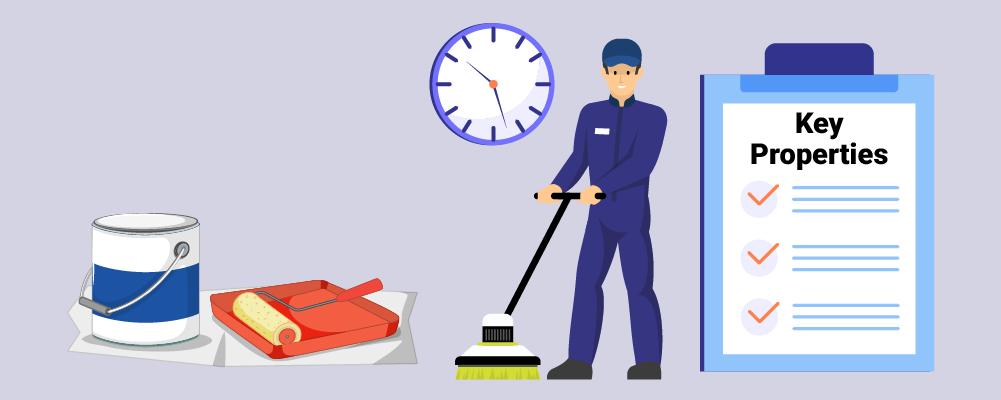
Epoxy resins have many key properties that make them fantastic for their many multi-uses, thus making them much more desirable and usable than a majority of other components that may otherwise have been used in their place in the past.
More and more people and industries turn to epoxy resins now, whereas, in the past, builder’s silicone and glue hardeners would have stood where epoxy now does in construction and industrial scenes.
These key properties help you to understand just why it has replaced these components.
High Strength
High strength as a property for epoxy resin is ideal for high-pressure containment application with minimal usage. It has a high contact strength which is able to seal joints and compression fittings when it comes to construction emergencies.
It can also serve as an ideal way to save structural repairs on a temporary basis. It is also ideal in marine settings in order to seal water leaks temporarily for up to 6 months, this tells you just how high in strength epoxy can be.
Minimal Shrinkage
Minimal shrinkage as a property for epoxy resin is mostly applied to marine and engineering-based settings. This can apply to the plumbing industry and ones like this.
Minimal shrinkage allows it to keep its stature. In comparison to previously used compounds such as silicone, epoxy resin does not shrink so much.
Silicone would shrink drastically, which in a plumbing setting can cause strength issues and sealing issues.
Epoxy resin does not suffer from this problem as it retains its form and does not degrade in such a dramatic way.
If epoxy were to shrink, and you have metal wood or plastic contacts together, then everything will come undone as it cracks due to the weight or gravity against it.
With epoxy not shrinking significantly, it holds these structures in place and prevents potential catastrophes in marine use scenarios.
Superior To A Variety Of Substrates
Epoxy resin is not necessarily superior in the sense that you may regard superiority, but it has more uses, it is more versatile, and it has higher strength with less shrinkage, so it does have advantages over other substrates.
It also has advantages in its shorter cure time. For example, silicone can dry within 48 to 72 hours while epoxy resin usually takes 8 to 16 hours. Though this does depend on the type of epoxy resin you are using.
So while it is not necessarily superior in every sense of the word, epoxy resin is advantageous in its versatility, strength, lack of shrinkage, and also in its shorter cure time which is most definitely ideal in an emergency.
However, it is not always superior as it cannot be used in every scenario i.e. it cannot be used in a freshwater system, so it has its downfalls as well.
Electrically insulating
Epoxy resin is not the most used component in electrical insulation, however, it does have some uses. The use of epoxy resin allows for protection in electrical components against dust, short circuits, and moisture.
This is known as standard epoxy resins actually have a much stronger thermal conductivity than air, so they provide more efficient dissipation of heat from the various components. This can potentially prolong service life.
However, this is not always standard, and many electricians have not taken to using epoxy in this fashion yet, but it is probable and has potential in the use of epoxy resin in insulation for electronics.
Chemical And Solvent Resistance
Epoxy resin is ideal when it comes to seeking out chemical and solvent resistance. If you need something that will be resistant to many things.
Epoxy is resistant to solvents in a massive way, however, epoxy CANNOT be put on top of a solvent. It is also highly resistant to chemicals, or at least most of them; however, like most things, it is not resistant to acid.
That being said, there are very few things out there that are resistant to acid!
However, there are some epoxy resins, such as one specially made two-part component epoxy, which was able to withstand a hard acidic environment.
This included being immersed in an environment of 96-98% sulfuric acid and 36% hydrochloric acid for a full year!
Do note that this epoxy was made to do this, most standard epoxies would not be able to survive these environments.
Low Toxicity
In a majority of scenarios epoxy resins are very low toxicity in a majority of terms. However, epoxies cannot be used in any environments made for consumption, so it would not be ideal for a water tank or plumbing as it would be dangerous.
That being said it is unlikely to release any chemicals at all after it is cured. And airborne it is mostly safe.
In terms of aquatic use, it is able to be used in waters with high water density such as marine uses, but it is not ideal for plumbing or use around waters meant for ingestion.
Low Cost
In comparison to alternatives, epoxy resin is very cheap, however, it is still more expensive than polyester resins. However, polyester resins do not have all the advantages that epoxy resins do.
You can buy epoxy resins from places like eBay and Amazon, or your local hardware store. Typically, you could be spending anywhere from $50 to around $120 per liter of epoxy.
However, it is always best to buy in bulk as it will be cheaper. But, what makes it even cheaper is the minimal amount you need per use. So, when you do buy epoxy in bulk, you can be guaranteed that it will last you quite a while.
If you used a 500 ml tub of epoxy resin for engineering work, and you used it on a daily basis, it would last you a good week at least. This would only cost you around $25 per purchase.
In comparison to some other alternatives, this is quite the cheap buy!
What Is Epoxy Resin Used For?
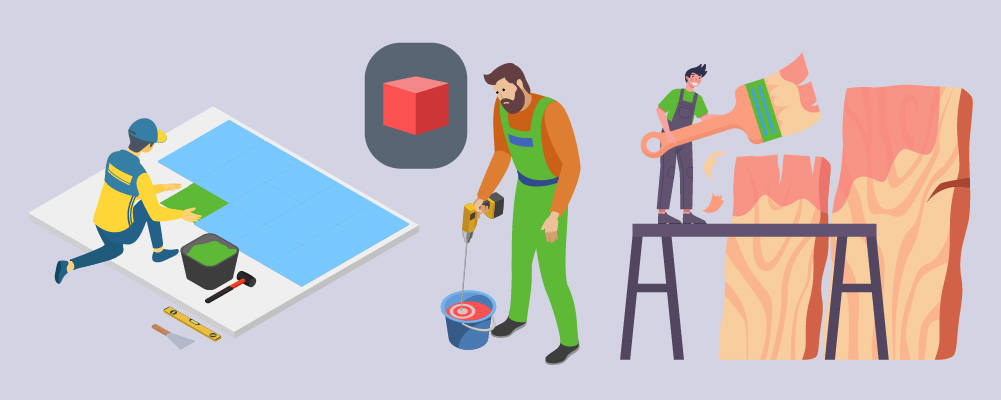
Epoxy resin has many uses as we already know. However, let’s look over some of its main uses. While the internet shows us the regular use of epoxy resin in a creative way, we want to focus on its industrial uses.
Adhesives
One of the many popular uses for epoxy resin is adhesion. It is very well known for being a very strong adhesive. It is a versatile product used in many different industries.
It will offer heat resistance and resistance to chemicals which makes it absolutely ideal for any products for anyone who needs a strong hold in spite of a lot of pressure.
This resin is also very durable, meaning that it is viable in use with a multitude of materials, such as fabric, wood, metal, glass, china, and so on. However, it is not really considered to be collectively water-resistant.
Electronics And Electrical Systems
Epoxy resin is also taking up some space in the electronics industry. It is used in insulator production, transformers, motors, and generators.
As these resins are brilliant at insulating, and since they offer protective properties from short circuits, dust, and moisture, it is still one of the primary products that are used in circuit creation as well.
Epoxy resins are valued for their many insulating properties and how they can function and offer protection in harsh environments. So they have a lot of different uses in electrics, and they may find more in the future as well.
Painting
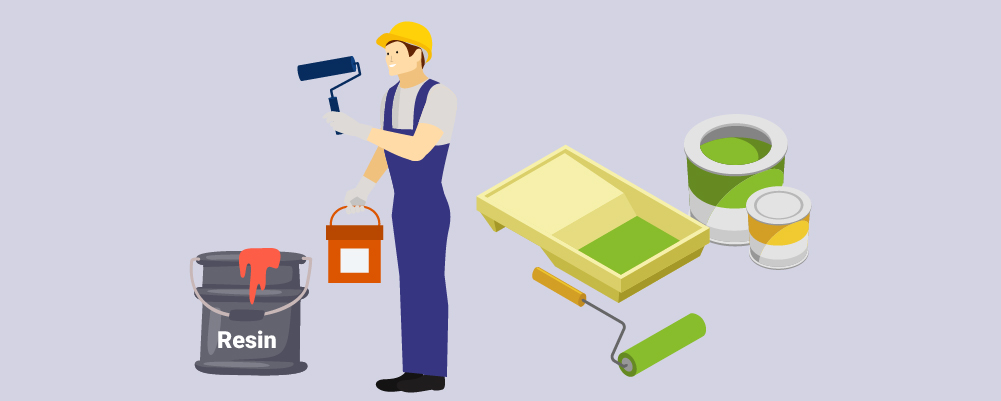
Epoxy resin is also finding its way into painting too. Otherwise known as ‘powder coating’ epoxy paint is found in many household goods, washers, dryers, stoves and so on.
This is a type of epoxy often used in commercial settings. It has a watery clean-up and offers a protective, tough coating, this paint is a brilliant option for many household kitchen based and cleaning based appliances.
This is similarly seen with cast iron, cast steel, and cast aluminum, these are all metals which are known to work very well with this particular painting application.
Coatings And Sealant
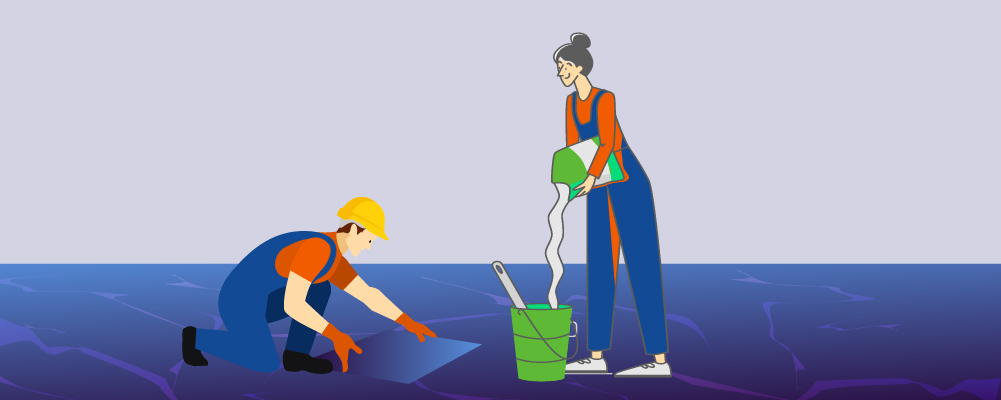
Epoxy is well known for being a corrosion preventative, it makes it an ideal solution for many household objects, especially those which may otherwise rust over the duration of time.
This often includes metal containers, paint cans, and foods which are often acidic, these are generally coated before they are used.
However, it is also used in the decorative flooring industry, such as terrazzo flooring, chip flooring, and any other aggregate flooring options. These are covered with an epoxy resin coating as well.
Epoxy flooring options are an environmental friend option in comparison to traditional flooring options as it minimizes the needs for water consumption and pesticides.
Repairs
Epoxy resin is also often used for repairs, due to its strong adhesive properties, a vast amount of consumers will use epoxy resin for the repair and maintenance of household appliances and objects.
This includes fragile items like glass, china, and ceramic. It can help secure snapped, and broken items to their original glory.
Epoxy resin is also able to be used on a vast amount of other materials in a similar way.
Thanks to the use of epoxy resin over what would otherwise be fragile items, you can create a very thin and tight barrier to securely hold these items in place for years.
Industrial Tools
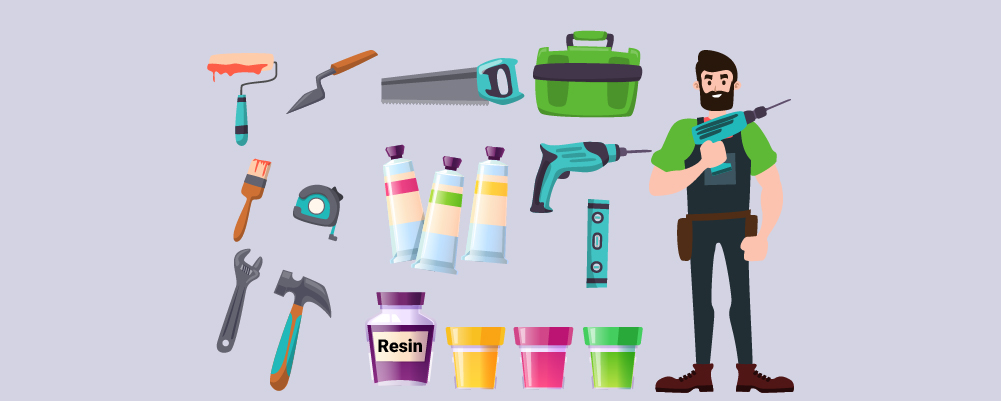
Epoxy resin can also be used to create tools, making tool creation a bit cheaper than it would otherwise be. Epoxy resin could make models, castings, molds, fixtures, and laminates.
Plastic epoxy tool is a brilliant alternative for metal or wood items which can be harder to maintain and more expensive to make.
In a majority of industrial processes, epoxy tools actually increase and enhance efficiency and generally reduce the overall cost and lead times that many industries end up wasting.
Casting
Epoxy resin can also be found in good use for casting, and artwork. Many artists and creatives will use epoxy resin as a way to be creative in artistic applications. Layers can be added as you create pictures.
You can see examples of this all over the internet. You could also decorate jewelry or even make jewelry from epoxy. Similarly, you can decorate or decoupage work surfaces as well.
Epoxy Resins And Woodworking
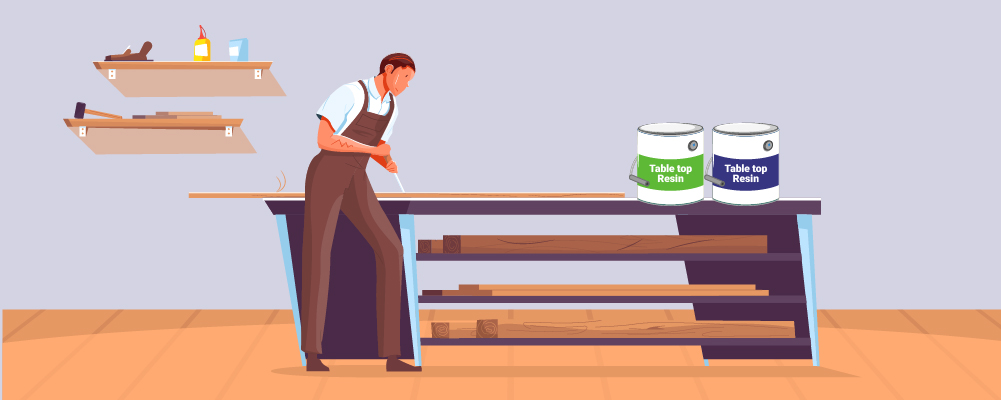
One common application is to use epoxy resin with wood. It is actually one of the most useful products to have in your woodworking shop. It is a powerful glue that can be used on a wooden surface and can also look very glamorous as well.
You can do quick repairs or glitz up some wood to make really aesthetically pleasing pieces of home artwork and furniture that might otherwise be bland.
How To Coat Wood Using Epoxy Resin
To create a wood coating with epoxy resin you want to start off by preparing the surface.
You need to create a clear coating, so you want to prepare the surface. Keep the surfaces clean, dry, and contaminant free. Sand the surface down and vacuum up any dust to avoid bubbles, damage or blister to your coating.
To get an even clearer coating, you want to sand with grain to enhance it. Teak and other oily woods need to have their surface oils removed with paper towels and acetone.
The environment should also be dust free and around 18 degree Celsius to be comfortable.
Never apply cold epoxy to a surface that is being heated.
Once you have prepared your surface properly you want to apply the epoxy. You should apply a few thin coats, instead of a singular thick one, thus applying it slowly and evenly.
Try using the roll on and tip off way of applying this. Roll a layer on with a foam roller and tip it off by dragging another over, cut it into sections to leave the surface totally level and free from any bubbles.
Then with some coarse grain timbers the first coat can be rough, lifting some wood fiber from the surface.
If this should occur, then stop and allow it to cure before you sand the surface until it is smooth and prepared for the next application.
Once the epoxy is on there like a mask, apply the next coat. If you are unable to even make a fingernail impression in the epoxy, wait until it has cured and then wash any blush amine away before you prepare for the next coat.
If you have bubbles in the surface, warm the surface, and it will reduce the viscosity, which will allow the air to escape better.
Always prepare surfaces and make sure the surface is dry free of dust and any contamination and is thoroughly abraded. Applying multiple thin coats will allow a smoother application.
Check this article to know more about how to use epoxy with wood.
How To Cast Epoxy Resin In A River Table
Before you start casting an epoxy resin in a river table, you will need to gather some materials.
- Clear epoxy resin.
- Wood (we recommend English Yew wood).
- Tinting pigments (translucent).
- Tape,
- Polishing compound and oil.
- Digital scales.
- Safety gear/ PPE.
- Epoxy adhesive.
- Mixing cups and buckets.
- Mixing sticks.
- Spreader.
- Various tools.
- Polypropylene sheeting.
- Hot melt glue gun.
Ensure your environment is dry and heated with a 20 degree Celsius ambient temperature. Your resin needs to be at a room temperature, it cannot be damp or cold as it can affect the result.
When you choose your wood, ensure it is seasoned, flat and dry. Whatever type and style you use is up to you.
You can then cut down and prepare it, but if you do not have the equipment to do so, ask your supplier to do this for you, so it is the right depth and size.
Then flip and invert the pieces to create a channel for a river and remove bark from the edge, then choose to remove the bark and rub it down with paper abrasive to remove loose materials.
Check for cracks, gaps, and knotholes then seal with resin.
Use tape to seal cracks to prevent resin coming out.
Overfill gaps with resin slightly and leave to cure.
Position wood slabs for your river, begin with a flat sheet, and use a suitable product to cut a base and sides to make a container around it. Use your glue gun to ensure your container is water tight and test it to ensure it is.
You can tint your resin or leave it as it is, many makers will use glow powders, pigments, and embed things in resin rivers, but always test out what you want to do in a small amount before you do it.
Measure and color your resin, ensure it is weighed to the right amount, and add the pigment to the resin, then add in hardener and the pre colored resin and mix, then transfer to another bucket and mix once more.
Pour a base layer to seal the under wood and minimize air bubbles, ensure it covers the whole base area and then place your wood planks in the right area. Seal the edge and top surface to fill knots, cracks and splits.
Then pour the first layer, measuring out your pigmented resin, mix and then pour it into your river channel and use a heat gun to remove bubbles. Leave it to cure then repeat for a second layer. Repeat until full.
Do not forget to finish off by routing and sanding your table once fully cured. You can use whatever technique makes the most sense to you, such as a route over a slab on a bridge, or a drum sander. Do not forget to sand and polish it off.
Summary
Epoxy has a multitude of applications in creative ways and throughout multiple industries. It has taken the place of many sealants and other compounds.
You should be careful when applying epoxy resins, regardless of type. Avoid it getting in your eyes, on your skin, and breathing it in.
While most epoxy is safe, it is always best to be cautious. There are so many types of epoxy to choose from as well, so make sure that whatever you choose is the right fit for what you need it for!